Yeah, I went a bit overboard. After hearing another forum member, Dan I think, having issues with the 5/8 inch butcher block splitting I wanted to provide good support. I got the other one shellacked and hopefully soon will be applying the Bee'Nooba wax to the outside.
@silverD said:
Yeah, I went a bit overboard. After hearing another forum member, Dan I think, having issues with the 5/8 inch butcher block splitting I wanted to provide good support. I got the other one shellacked and hopefully soon will be applying the Bee'Nooba wax to the outside.
I was thinking of using four of the GD-40-FBL casters per speaker to aid in moving them to and from listening position. Do you think mounting them to the bottom will provide enough stability or will a base or outriggers be needed?
That reminds me. Locally we have a builders outlet type place. Last time i was there they had stacks of acacia countertop for not outrageous prices. But that was a few years ago.
I picked up 2 chopping blocks. I had to sort through to find the best ones and to be honest the quality isn't that great, but hopefully they work out. Here's a before and after of sanding and applying the hard wax oil.
The chopping blocks have an interesting construction with the tops and bottoms that are wider, but much thinner then the middle boards. When I went to another Aldi, I found some boards that were simply two boards thick without the thin tops and bottoms. Because of the end grain and the recessed handles, I think I'll stick with the flat fronts. I'm a bit afraid to cut the boards to remove the recesses in case I uncover voids. Here are the two blocks stacked but one rotated by 90 degrees.
I was thinking the same thing Wolf, but I think I like the smooth front over the end grain. Haven't made a final decision though. What I did accomplish was filling one speaker with acoustic damping.
So it's been a while and no updates. That's because my two months off for the summer came to an end and the house build is closing in on completion while the punch list for the builder is growing by the day. I haven't made much progress on the oak slabs that are to be used for the dining room table until recently. I built a kiln to hopefully heat the boards up to a 140° to kill off any beetle inhabitants that Steve had spotted. I even found a few holes in the Quarters which has me bummed.
Eggguy's table pics in another thread reminded me to post some of mine. Post kilning, I shortened them to 8 ft for transport and to make them easier to flatten. They are now 2" thick. I need to get around 15" of width on each to make the 44" wide table.
I was planning on having the guy who flattened them cut them down to size and glue them, but I guess he just had a big order come in and won't have the time until December. I don't own a track saw to do this myself. Suggestions?
Get it close with a straight edge+circular saw. Then clean it up by repositioning the straight edge as a guide for a top-bearing trim router bit. After the first pass, can use the newly trimmed edge as the guide for the next deeper pass since it is a thick board. Seems best to use a stout piece for straight edge due to the long length. Such as the fresh factory edge of an MDF board if that can be trusted. Poor man's edge jointer technique.
Comments
shoehorned that garden hose into the speakON > nice fit
One inside shellacked.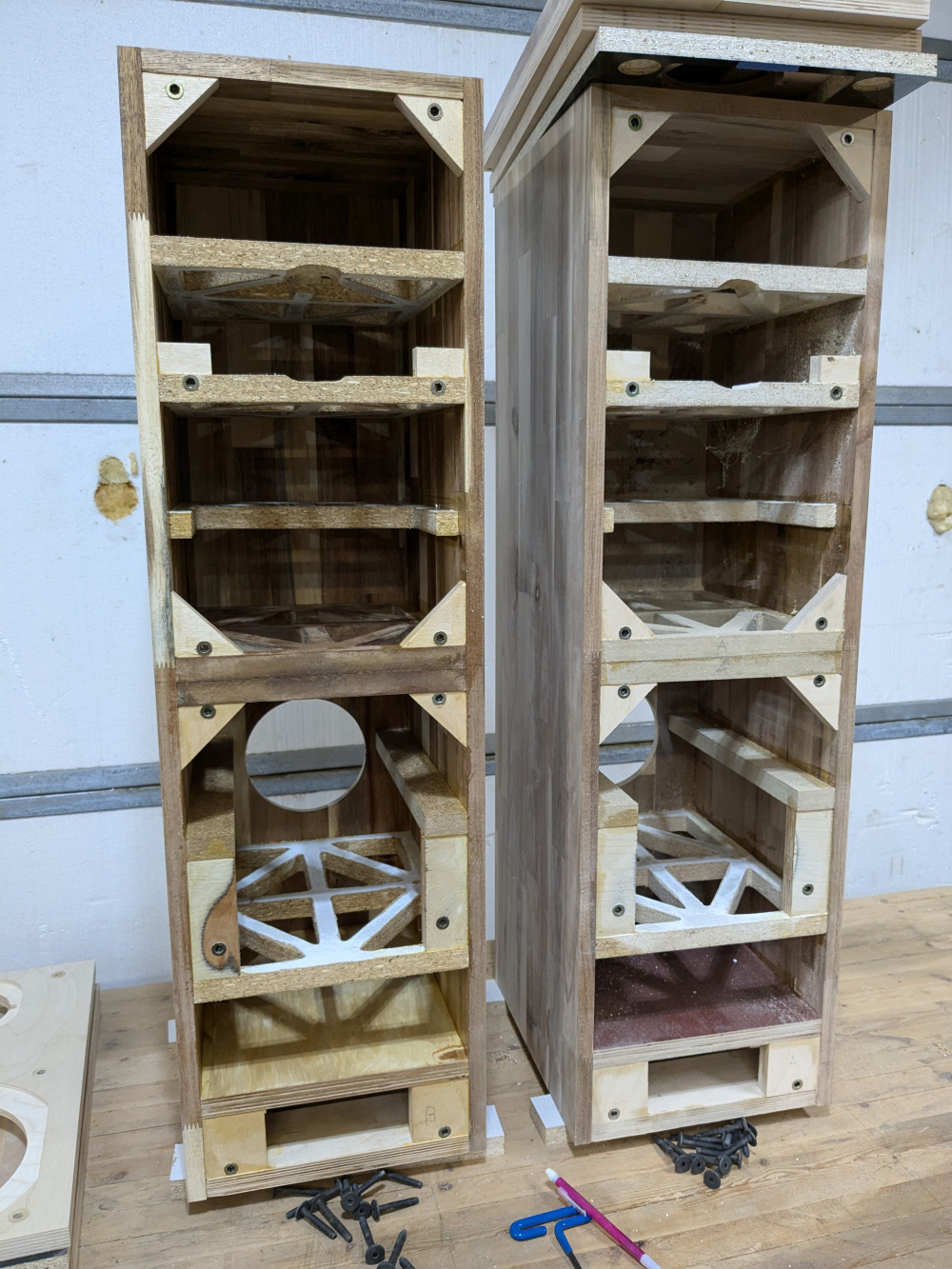
Are these also pillars to support an upstairs apartment?
Needs wheels and a set of handles on the rear/top corner like hand-trucks . . .
Tell me you are worried about rigidity without telling me you are worried about rigidity.
Yeah, I went a bit overboard. After hearing another forum member, Dan I think, having issues with the 5/8 inch butcher block splitting I wanted to provide good support. I got the other one shellacked and hopefully soon will be applying the Bee'Nooba wax to the outside.
No such thing as too braced.
I was thinking of using four of the GD-40-FBL casters per speaker to aid in moving them to and from listening position. Do you think mounting them to the bottom will provide enough stability or will a base or outriggers be needed?
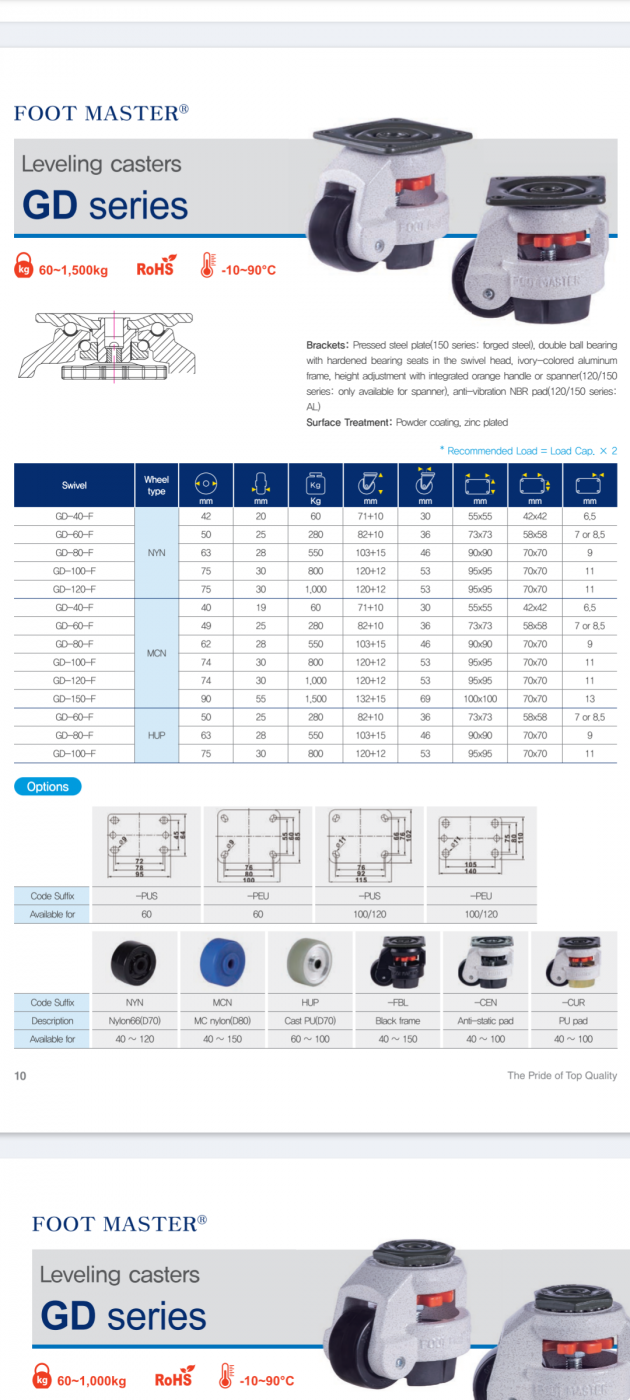
First coat of hard wax oil applied.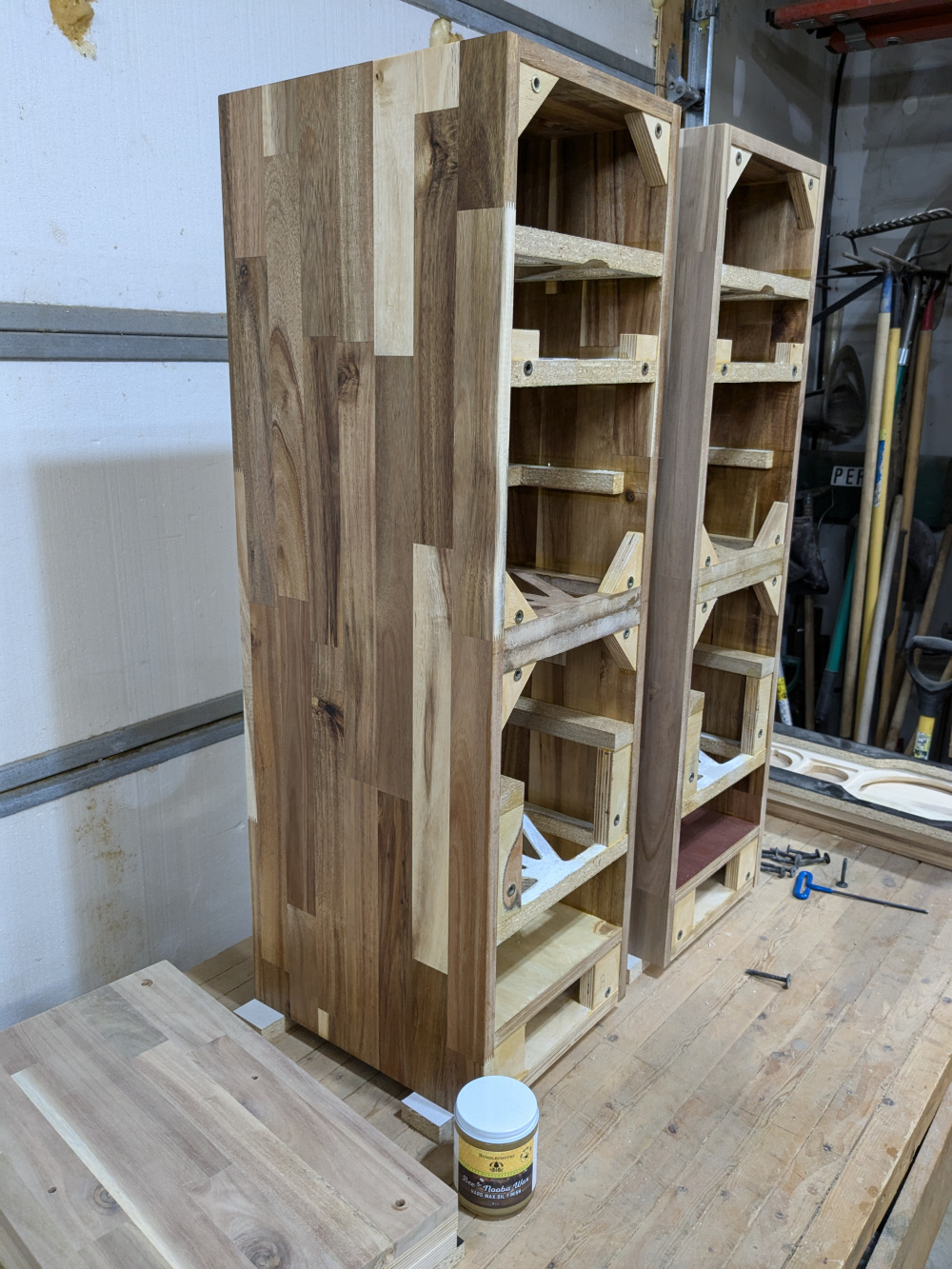
Outriggers for sure - you could snag a wheel and tip over while moving those narrow boxes if mounted underneath.
I will look into some aluminum CNC'd outrigger plates to mount the casters to. I applied a second coat of hard wax oil to the cabinets.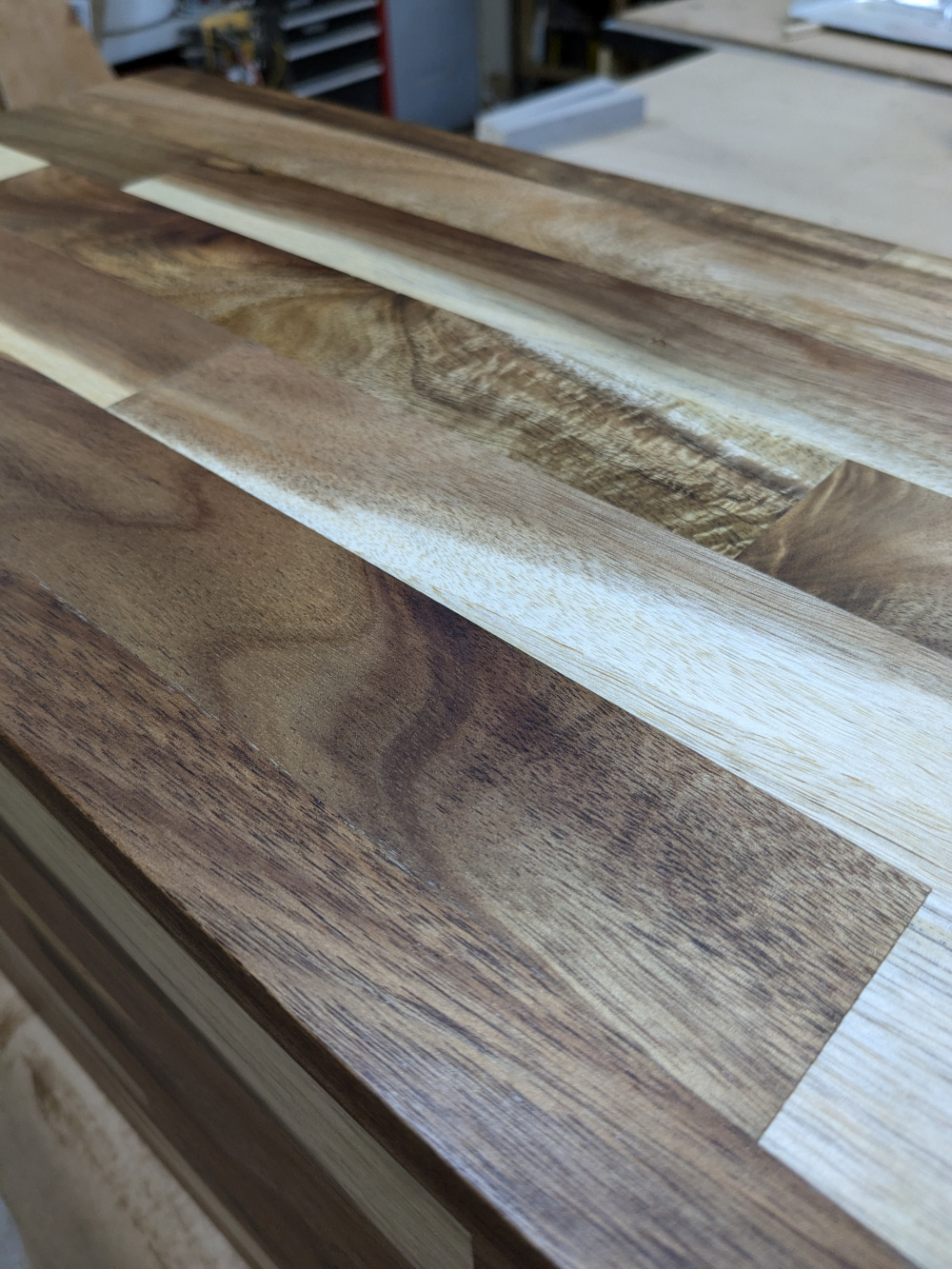
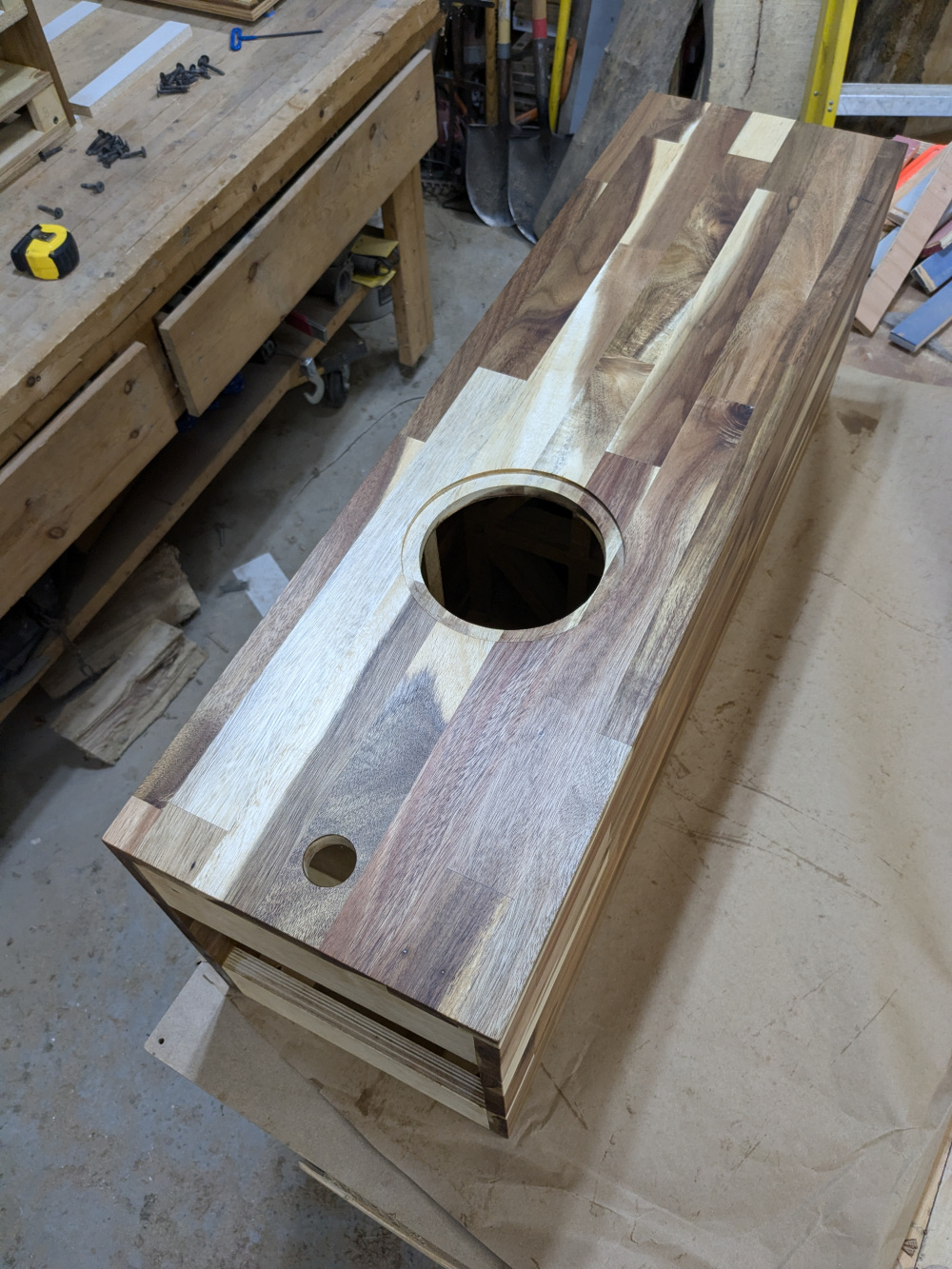
Nice😎🤘🏼
What do you know, Aldi will have these chopping blocks which includes a 15.75" x 15.75" x 1.57" acacia square option tomorrow! https://www.aldi.us/weekly-specials/upcoming-aldi-finds/upcoming-aldi-finds-detail/ps/p/croftonwooden-chopping-block/
That reminds me. Locally we have a builders outlet type place. Last time i was there they had stacks of acacia countertop for not outrageous prices. But that was a few years ago.
Yep, I haven't been there, but a local one has 25" x 96" acacia butcher block tops for $225: https://bmomn.com/wp-content/uploads/2023/05/ButcherBlockPricing2123.pdf
I picked up 2 chopping blocks. I had to sort through to find the best ones and to be honest the quality isn't that great, but hopefully they work out. Here's a before and after of sanding and applying the hard wax oil.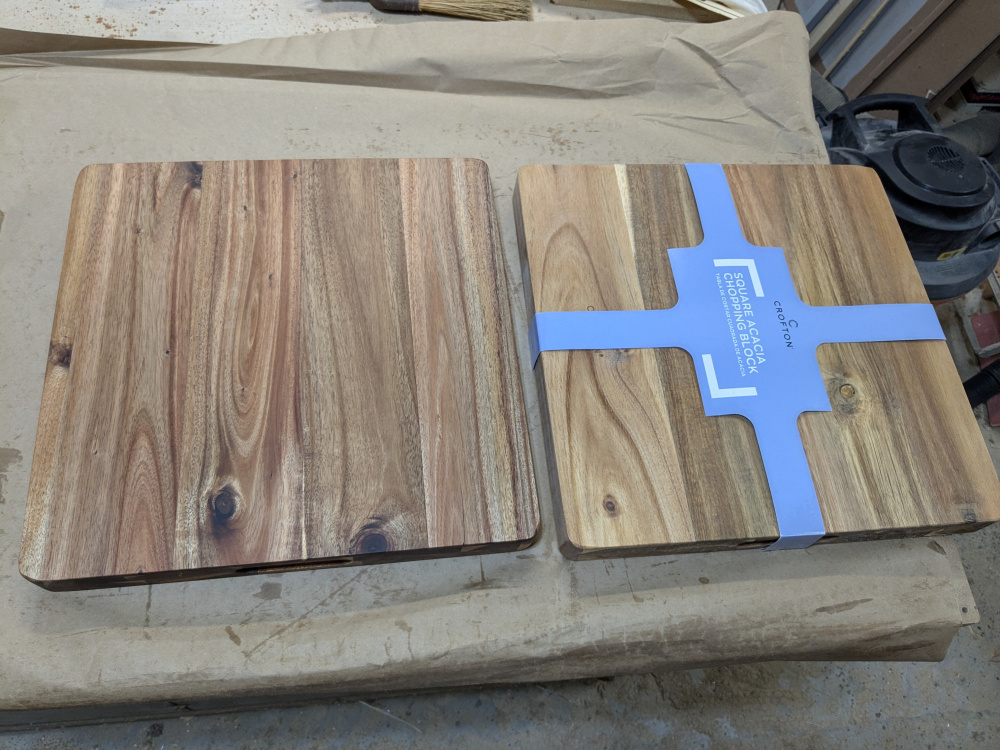
Here is a what they would like like with the chopping blocks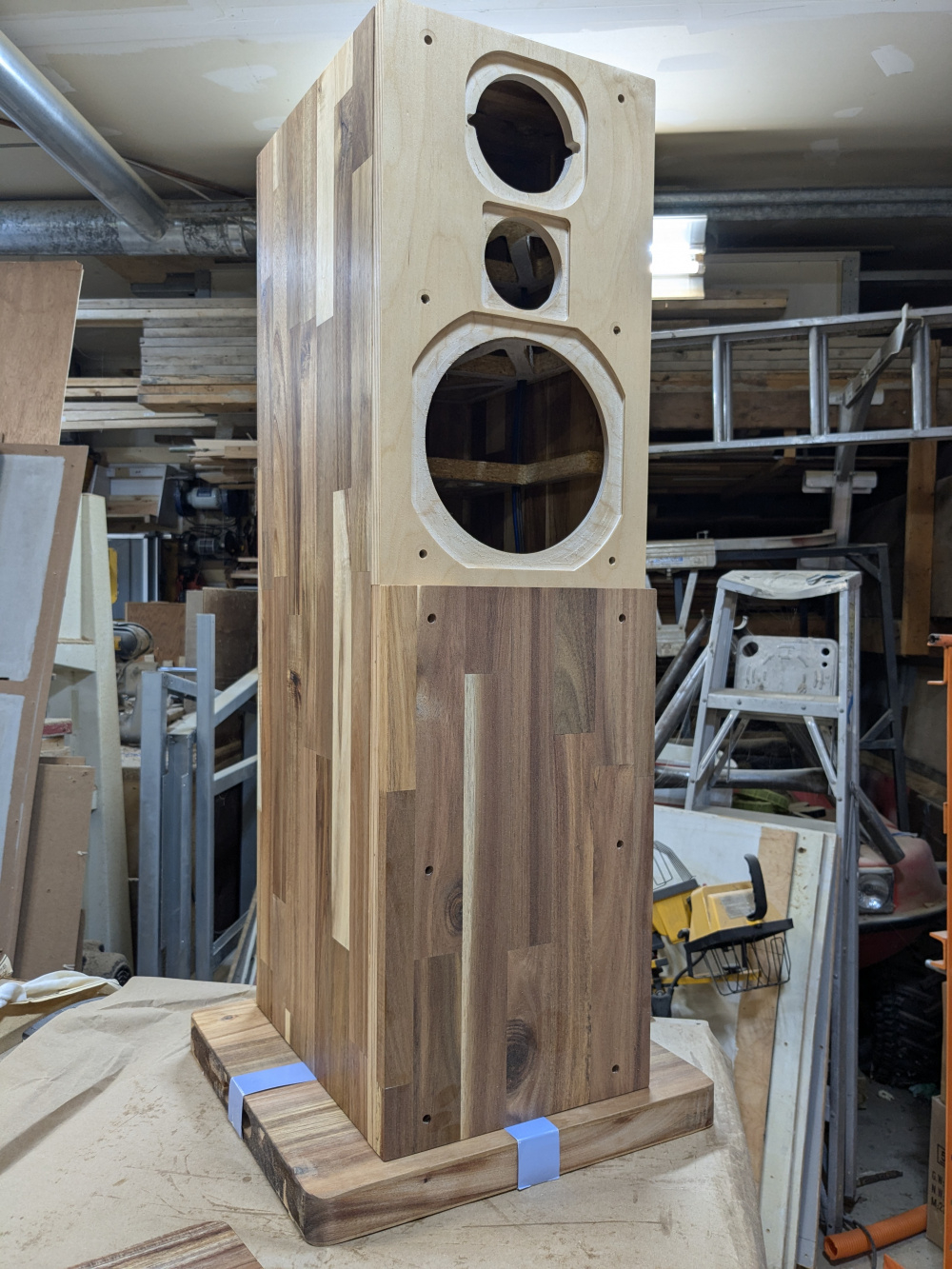
You could route some recesses in the bottom to install your casters so that they don't sit so high.
That base looks really nice. Blends very well with the upper cabinet.
Adds more beef to the beef.👍🏻
I'd like to see it with the grain front to back.
+1
The chopping blocks have an interesting construction with the tops and bottoms that are wider, but much thinner then the middle boards. When I went to another Aldi, I found some boards that were simply two boards thick without the thin tops and bottoms. Because of the end grain and the recessed handles, I think I'll stick with the flat fronts. I'm a bit afraid to cut the boards to remove the recesses in case I uncover voids. Here are the two blocks stacked but one rotated by 90 degrees.
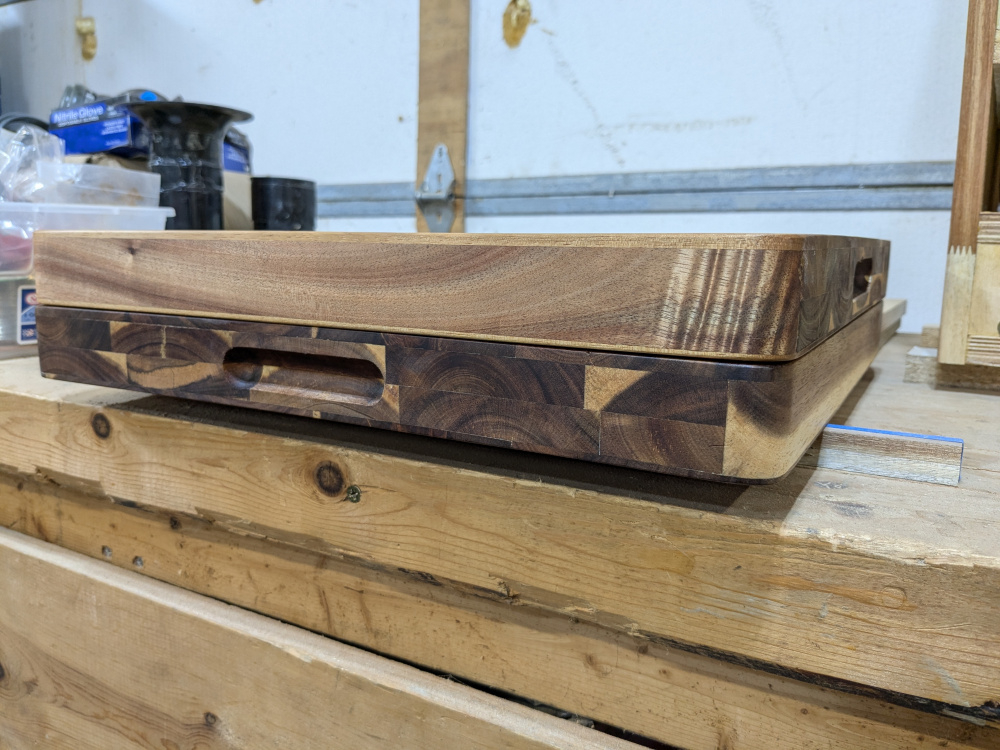
You could always place the name badges in the handle area.
InDIYana Event Website
I was thinking the same thing Wolf, but I think I like the smooth front over the end grain. Haven't made a final decision though. What I did accomplish was filling one speaker with acoustic damping.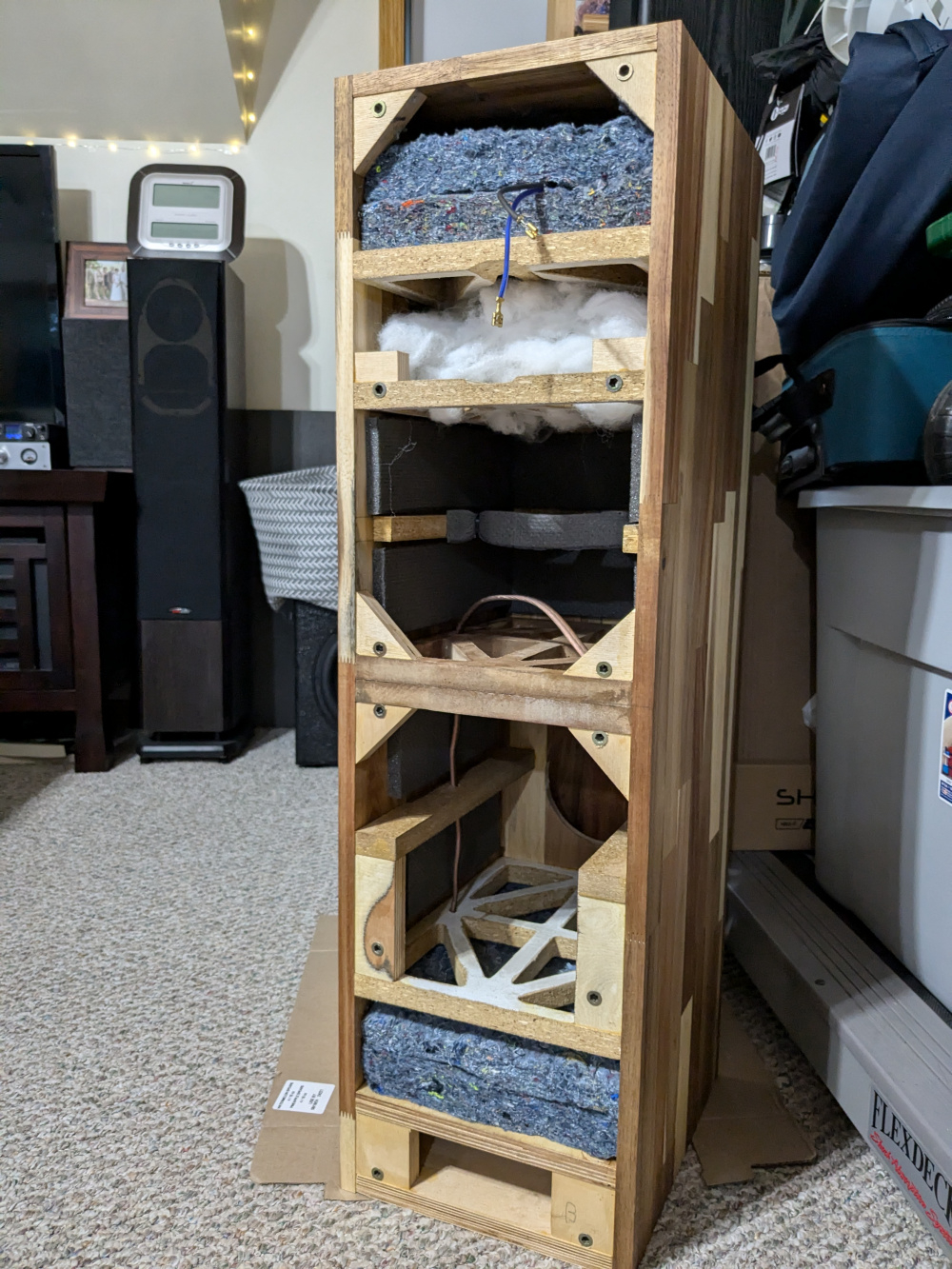
So it's been a while and no updates. That's because my two months off for the summer came to an end and the house build is closing in on completion while the punch list for the builder is growing by the day. I haven't made much progress on the oak slabs that are to be used for the dining room table until recently. I built a kiln to hopefully heat the boards up to a 140° to kill off any beetle inhabitants that Steve had spotted. I even found a few holes in the Quarters which has me bummed.
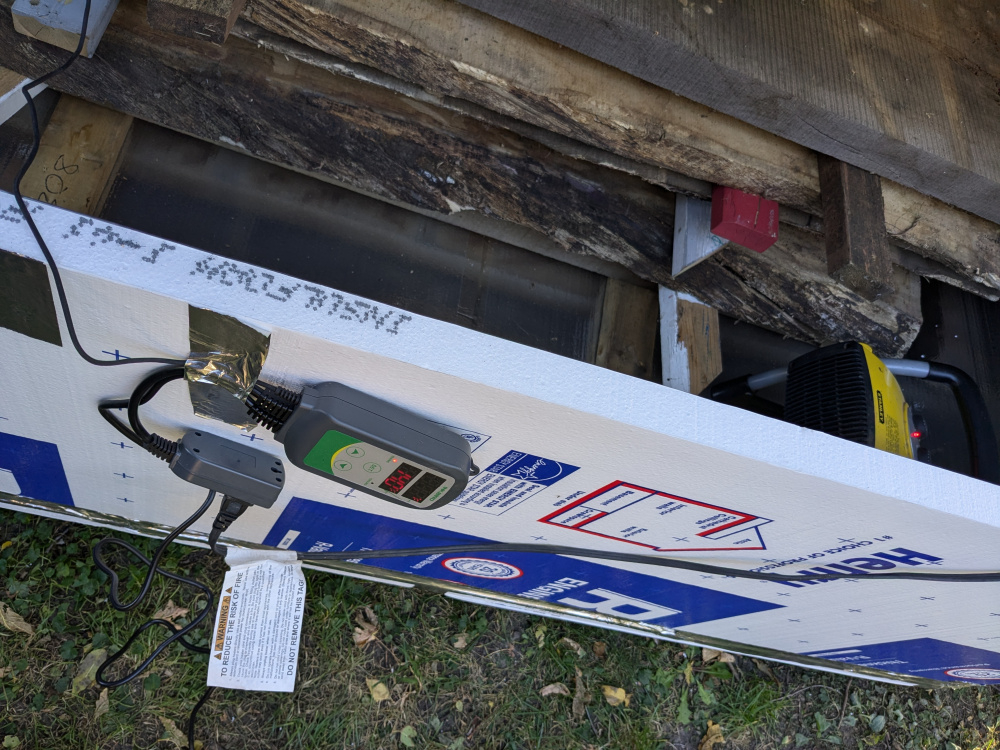
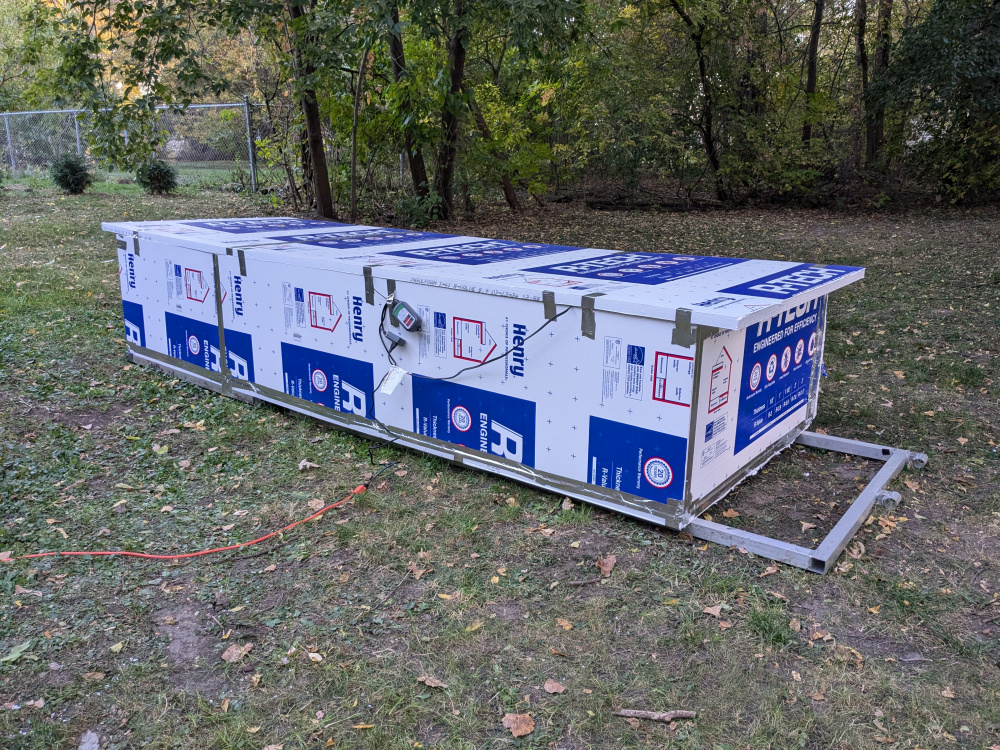
Very industrious!
Eggguy's table pics in another thread reminded me to post some of mine. Post kilning, I shortened them to 8 ft for transport and to make them easier to flatten. They are now 2" thick. I need to get around 15" of width on each to make the 44" wide table.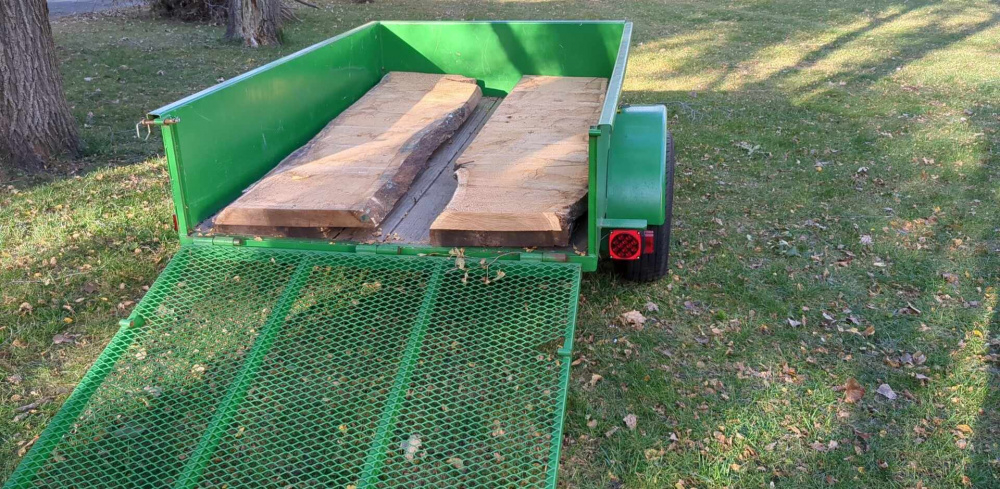
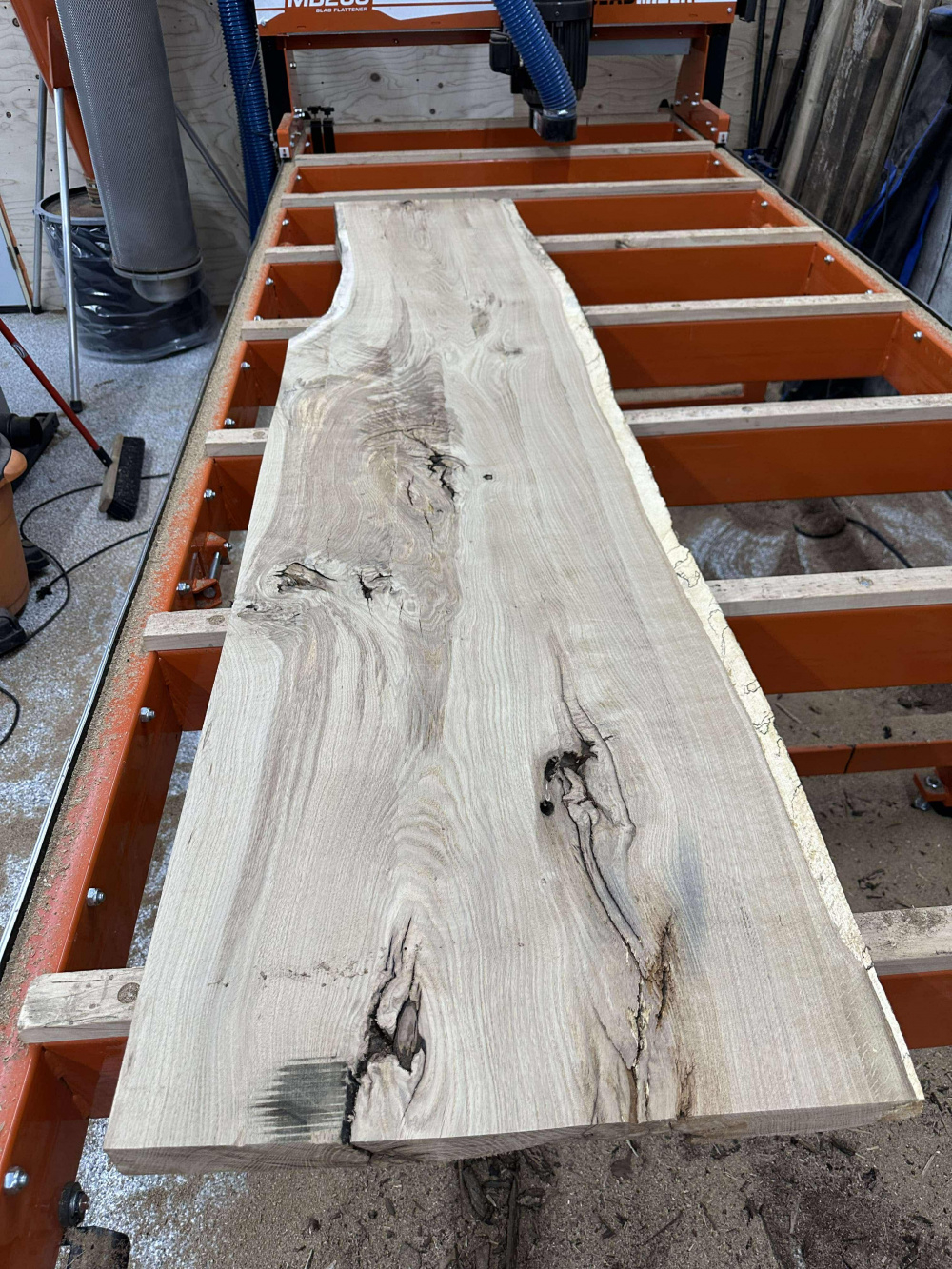
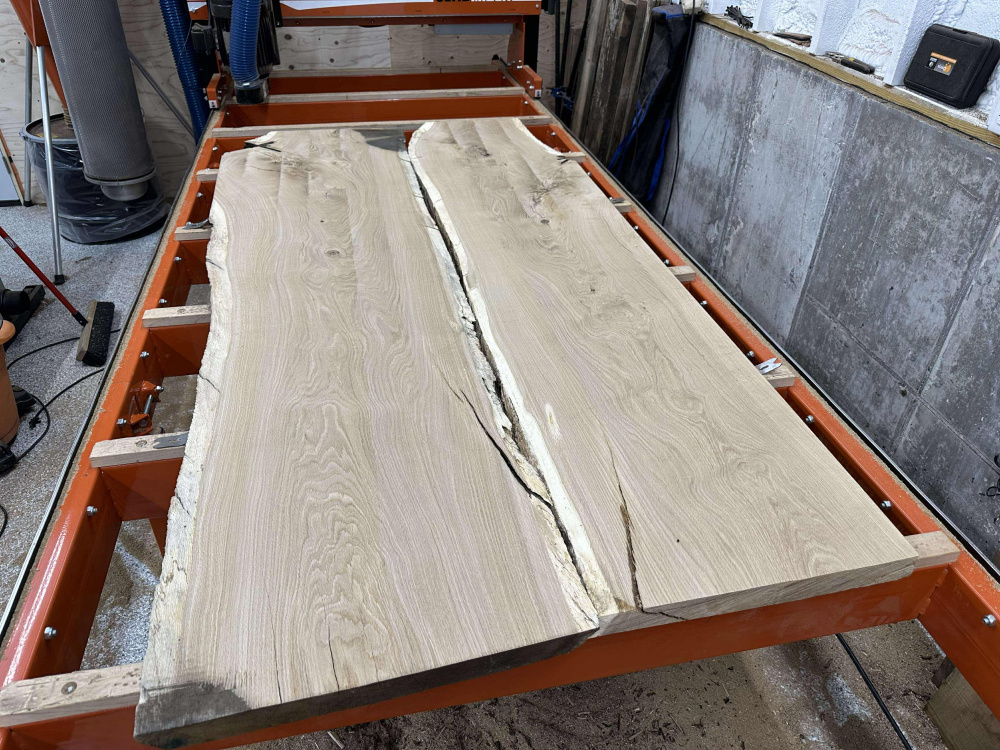
More pics please as you proceed
I was planning on having the guy who flattened them cut them down to size and glue them, but I guess he just had a big order come in and won't have the time until December. I don't own a track saw to do this myself. Suggestions?
Get it close with a straight edge+circular saw. Then clean it up by repositioning the straight edge as a guide for a top-bearing trim router bit. After the first pass, can use the newly trimmed edge as the guide for the next deeper pass since it is a thick board. Seems best to use a stout piece for straight edge due to the long length. Such as the fresh factory edge of an MDF board if that can be trusted. Poor man's edge jointer technique.